Unlocking Operational Excellence: Your Guide To Standard Operating Procedures
In the dynamic landscape of modern business, where efficiency, consistency, and quality are paramount, the concept of a "protocolo operacional padrão" (standard operating procedure or SOP) emerges as a non-negotiable cornerstone for success. Every enterprise, regardless of its size or industry, grapples with the need to execute tasks repeatedly, ensuring each iteration meets predefined benchmarks. It's in this quest for unwavering reliability and peak performance that SOPs prove their indispensable value, serving as the very backbone of streamlined operations and robust quality management.
From the intricacies of food handling to the complexities of healthcare and manufacturing, a "protocolo operacional padrão" acts as a meticulously crafted blueprint, guiding teams through their daily responsibilities with precision and clarity. It's more than just a document; it's a strategic asset designed to standardize processes and workflows, ultimately safeguarding quality, boosting productivity, and ensuring uniformity in the products and services offered. This comprehensive guide will delve into the essence of SOPs, exploring their profound importance, key objectives, and the practical steps to implement them effectively within your organization.
Table of Contents
- What is a "Protocolo Operacional Padrão" (SOP)?
- The Undeniable Importance of SOPs in Business
- Key Objectives of Implementing SOPs
- Legal and Regulatory Compliance: SOPs as a Safeguard
- Types and Examples of SOPs
- Crafting Your Own SOP: A Step-by-Step Guide
- Benefits Beyond Standardization: The Ripple Effect of SOPs
- Embracing the Future with SOPs: Continuous Improvement
What is a "Protocolo Operacional Padrão" (SOP)?
At its core, a "protocolo operacional padrão" is a meticulously written document that details specific actions, sequences, and rules for how a particular task or process must be carried out within an organization. It is, in essence, a roadmap for your team, ensuring that all employees perform tasks consistently, safely, and in compliance with regulatory or internal standards. As the "Data Kalimat" aptly states, "O procedimento operacional padrão (pop) é um documento estratégico que deve ser criado para todas as atividades de uma empresa." This highlights its pervasive nature, touching every facet of an organization's operations.
The objective of an SOP is to provide clear, step-by-step instructions for routine and specific operations. It details the activities and routines, providing information about the order of procedures, materials utilized, and working parameters. Think of it as the institutional memory of your company, capturing best practices and ensuring that critical knowledge isn't lost when personnel change. It's a tool where all necessary information for carrying out a procedure is recorded, standardizing the activity simply so that it is always executed in the same way. This consistency is not merely about uniformity; it's about predictable outcomes, reduced errors, and enhanced reliability.
The Difference Between POP and Protocol
While often used interchangeably, especially in a broader sense, it's worth noting the subtle distinction between a "Procedimento Operacional Padrão" (POP) and a "Protocolo" in some contexts, particularly in healthcare or highly regulated environments. A POP, as discussed, is a detailed, step-by-step instruction for a specific task. A "Protocolo," on the other hand, might refer to a broader set of guidelines or a plan of action for a particular situation, often involving multiple POPs or a sequence of decisions rather than just a single, defined procedure. For instance, a "protocolo de atendimento de emergência" (emergency care protocol) would outline the overall approach to an emergency, which might then refer to various POPs for specific actions like administering medication or performing CPR. However, for the purpose of general business operations, "protocolo operacional padrão" and SOP are widely understood to mean the same thing: a standardized set of instructions for repeatable tasks.
The Undeniable Importance of SOPs in Business
The significance of a well-implemented "protocolo operacional padrão" cannot be overstated. It is a fundamental pillar of quality management and is inherently associated with the idea of standardization, and for good reason. Businesses thrive on predictability and efficiency, and SOPs deliver precisely that. They provide a clear, consistent framework for operations, which translates into a multitude of benefits. As the "Data Kalimat" emphasizes, "Entenda o que é pop (procedimento operacional padrão), como fazer, qual a sua importância e principais vantagens que ele pode gerar para a sua empresa."
Firstly, SOPs are crucial for ensuring consistency. In any business, especially those offering products or services, consistency is key to customer satisfaction and brand reputation. Imagine a restaurant where the same dish tastes different every time, or a service center where the quality of repair varies wildly. This inconsistency erodes trust and drives customers away. SOPs eliminate guesswork, ensuring that every task, from manufacturing a product to handling a customer inquiry, is performed to the same high standard, every single time.
Secondly, they significantly enhance efficiency. By clearly outlining the most effective way to perform a task, SOPs reduce wasted time, effort, and resources. They prevent employees from reinventing the wheel for every task, allowing them to follow a proven path. This leads to faster execution, fewer errors, and a more streamlined workflow, ultimately boosting overall productivity. When everyone is on the same page, working towards a common, well-defined method, the entire operation moves more smoothly and effectively.
Thirdly, SOPs are invaluable for training and onboarding new employees. Instead of relying on tribal knowledge or ad-hoc training, new hires can quickly learn their roles by following detailed, written procedures. This not only accelerates the onboarding process but also ensures that new team members are trained consistently and correctly from day one. It reduces the burden on experienced staff who would otherwise spend significant time explaining routine tasks, freeing them up for more complex responsibilities.
Finally, SOPs serve as a critical tool for problem-solving and continuous improvement. When an issue arises, well-documented procedures allow for easy identification of where a process went wrong. They provide a baseline against which performance can be measured and improved. By analyzing deviations from the "protocolo operacional padrão," businesses can pinpoint root causes of problems, implement corrective actions, and refine their processes for future success. This iterative improvement cycle is vital for staying competitive and adaptable in a changing market.
Key Objectives of Implementing SOPs
The implementation of a "protocolo operacional padrão" is not merely a bureaucratic exercise; it is driven by a set of clear and impactful objectives designed to elevate an organization's performance. The "Data Kalimat" highlights that SOPs aim to "garantir a qualidade, produtividade e padronização dos produtos e serviços oferecidos." These three pillars – quality, productivity, and standardization – form the core purpose of any effective SOP system.
Enhancing Quality and Productivity
One of the primary objectives of SOPs is to guarantee and enhance the quality of products and services. By defining precise steps, materials, and parameters, SOPs minimize variations and ensure that outputs consistently meet desired specifications. For instance, in food handling, the RDC 216/2004 of ANVISA defines a standard operating procedure as a "procedimento escrito de forma objetiva que estabelece instruções sequenciais para a realização de operações rotineiras e específicas na manipulação de alimentos.” This objective definition underscores the direct link between clear procedures and food safety and quality. When every employee follows the same validated method, the likelihood of errors, defects, or non-compliance significantly decreases, leading to higher quality outcomes and greater customer satisfaction.
Hand-in-hand with quality is the objective of boosting productivity. SOPs eliminate ambiguity and provide a clear path for task execution. This reduces the time spent on decision-making, troubleshooting, and correcting mistakes. When employees know exactly what to do, how to do it, and what resources to use, they can perform their duties more efficiently. This streamlined approach allows for more work to be completed in less time, optimizing resource allocation and ultimately contributing to the company's bottom line. The efficiency gained from a well-defined "protocolo operacional padrão" directly translates into improved output and operational effectiveness.
Beyond quality and productivity, SOPs are fundamental to achieving complete standardization. They ensure that "toda empresa possui processos que precisam ser executados repetidamente" are indeed executed in the exact same manner each time. This creates a predictable operational environment, which is crucial for scalability, auditing, and maintaining brand integrity. Standardization facilitates easier management, better control over outcomes, and a consistent customer experience across all touchpoints. It's about building a robust, repeatable system that doesn't rely on individual heroics but on collective adherence to proven methods.
Legal and Regulatory Compliance: SOPs as a Safeguard
In many industries, particularly those with high stakes like healthcare, pharmaceuticals, food production, and finance, a "protocolo operacional padrão" is not merely a best practice; it is a legal and regulatory requirement. Governments and industry bodies establish stringent regulations to protect consumers, ensure safety, and maintain market integrity. SOPs are the practical manifestation of how an organization meets these obligations, serving as verifiable proof of adherence.
The reference to RDC 216/2004 from ANVISA (Brazil's National Health Surveillance Agency) in the "Data Kalimat" is a perfect illustration of this. This regulation specifically mandates written standard operating procedures for food handling, demonstrating the critical role SOPs play in public health and safety. Without clearly documented procedures for hygiene, storage, preparation, and waste disposal, food businesses would struggle to prove compliance, potentially facing severe penalties, fines, or even closure. This applies equally to other sectors: pharmaceutical companies must have SOPs for drug manufacturing, healthcare institutions for patient care, and financial firms for transaction processing, all to meet regulatory demands.
SOPs act as a crucial safeguard, protecting the company from legal liabilities and reputational damage. When an incident occurs, regulatory bodies will often demand to see the relevant "protocolo operacional padrão" to assess whether established procedures were followed. If procedures are non-existent, outdated, or not adhered to, the company is exposed to significant risk. Conversely, well-maintained and followed SOPs demonstrate due diligence and a commitment to responsible operations, which can be invaluable in mitigating legal repercussions.
Furthermore, SOPs facilitate internal and external audits. Auditors rely on these documents to verify that processes are being executed correctly and that the company is meeting all necessary standards. A clear, comprehensive "protocolo operacional padrão" simplifies the audit process, making it easier to demonstrate compliance and identify areas for improvement before they become major issues. This proactive approach to compliance not only minimizes risk but also builds trust with regulators, partners, and customers.
Types and Examples of SOPs
The versatility of a "protocolo operacional padrão" means it can be created and utilized in diverse situations across various departments and functions within an organization. While the fundamental purpose remains the same—to standardize and guide—SOPs can be categorized based on their scope or the area they address. The "Data Kalimat" mentions, "Os mais usuais são pops por área e pops por tipo de processo." This distinction helps in organizing and managing the vast array of procedures that an enterprise might need.
SOPs by Area
These SOPs are typically department-specific or function-specific, detailing the routine operations within a particular division. Examples include:
- Manufacturing/Production SOPs: These would cover everything from machine operation and maintenance to quality control checks, assembly line procedures, and packaging instructions. For instance, an SOP for a specific machine might detail start-up, operation, shutdown, and troubleshooting steps.
- Human Resources (HR) SOPs: These could include procedures for employee onboarding, performance reviews, disciplinary actions, leave requests, and recruitment processes. An SOP for onboarding might detail the sequence of paperwork, system access, and initial training.
- Sales and Marketing SOPs: These might cover lead generation, customer relationship management (CRM) usage, sales pitch delivery, order processing, and marketing campaign execution. An SOP for lead qualification would define criteria and steps to assess potential customers.
- Finance and Accounting SOPs: Procedures for invoice processing, expense reporting, payroll, budget management, and financial reporting fall into this category. An SOP for accounts payable would detail the steps from receiving an invoice to issuing payment.
- Information Technology (IT) SOPs: These cover network security protocols, software installation, data backup and recovery, system maintenance, and help desk procedures. An SOP for password resets would provide clear, secure steps for IT support.
- Healthcare/Nursing SOPs: As mentioned in the "Data Kalimat," "os procedimentos operacionais padrão (pops) de enfermagem, confeccionados com base no preconizado por literatura atual pertinente, representam a descrição sistematizada e detalhada." These would include procedures for patient admission, medication administration, wound care, infection control, and emergency response.
SOPs by Type of Process
These SOPs focus on specific types of activities or workflows that might cut across different departments. Examples include:
- Safety SOPs: These are critical for any organization, detailing procedures for emergency evacuations, handling hazardous materials, using personal protective equipment (PPE), and accident reporting. An SOP for chemical spill cleanup would outline immediate actions, containment, and disposal.
- Quality Control SOPs: These define the steps for inspecting products or services at various stages to ensure they meet quality standards. This could include sampling methods, testing procedures, and criteria for acceptance or rejection.
- Maintenance SOPs: Procedures for routine equipment checks, preventative maintenance schedules, troubleshooting common issues, and repair processes. An SOP for daily machine inspection would list items to check and their acceptable conditions.
- Customer Service SOPs: These guide interactions with customers, covering call handling, complaint resolution, refund processes, and follow-up procedures. An SOP for handling a customer complaint might detail steps from logging the complaint to its resolution and follow-up communication.
Understanding these different types helps organizations systematically document all necessary procedures, ensuring comprehensive coverage and easy accessibility for the relevant teams. The goal is always to provide a clear, unambiguous "protocolo operacional padrão" that empowers employees to perform their duties effectively and consistently.
Crafting Your Own SOP: A Step-by-Step Guide
Creating an effective "protocolo operacional padrão" is a structured process that requires careful planning, clear communication, and attention to detail. It's not just about writing down steps; it's about designing a document that is practical, easy to follow, and genuinely useful for your team. The "Data Kalimat" encourages, "Aprenda a criar seu modelo de pop e padronize processos na sua empresa." Here’s a step-by-step approach to developing robust SOPs:
Essential Elements of an Effective SOP
Before diving into the writing, understand the core components that make an SOP effective:
- Title: Clear and concise, indicating the process it covers.
- Purpose/Scope: Briefly explain why this SOP exists and what it aims to achieve.
- Responsibilities: Clearly state who is responsible for each step or for the overall process.
- Definitions: Define any technical terms or acronyms used.
- Procedure: The heart of the SOP, detailing the step-by-step instructions.
- Materials/Equipment: List all necessary tools, materials, or software.
- Safety Precautions: Important for high-risk tasks.
- Quality Control/Checkpoints: How to ensure the task is done correctly.
- Troubleshooting: What to do if something goes wrong.
- References: Link to other relevant documents or regulations.
- Revision History: Track changes, dates, and authors to ensure the document is current.
The Creation Process:
- Identify the Process: Begin by identifying which processes need a "protocolo operacional padrão." Focus on critical, repetitive, or high-risk tasks. Consider areas where inconsistencies or errors frequently occur.
- Gather Information: Consult with the individuals who currently perform the task. They are the experts. Observe the process, ask questions, and document every step. Understand the nuances, common pitfalls, and best practices. This collaborative approach ensures the SOP is realistic and practical.
- Define the Scope and Purpose: Clearly articulate what the SOP covers and what it aims to achieve. For example, "This SOP outlines the procedure for processing customer returns to ensure consistent service and accurate inventory updates."
- Outline the Steps: Break down the process into logical, sequential steps. Use action verbs and keep sentences concise. Avoid jargon where possible, or define it clearly. For complex processes, use sub-steps or flowcharts.
- Add Details and Context: Include information about necessary materials, equipment, safety warnings, and quality checkpoints. Specify parameters (e.g., temperature settings, time limits). If a decision point exists, clearly outline the criteria for each path.
- Draft the SOP: Write the initial version of the "protocolo operacional padrão" using a clear, objective, and easy-to-understand language. Use bullet points, numbered lists, and tables to enhance readability. Visual aids like diagrams or screenshots can be incredibly helpful.
- Review and Validate: This is a crucial step. Have the draft reviewed by those who perform the task, their supervisors, and any relevant stakeholders (e.g., quality assurance, legal). Test the SOP in a real-world scenario to ensure it is accurate, complete, and practical. Make revisions based on feedback.
- Approve and Distribute: Once validated, the SOP needs formal approval, usually by a department head or management. Then, it must be effectively distributed to all relevant personnel. Ensure it is easily accessible, whether through a shared drive, an internal portal, or a physical binder.
- Implement and Train: Simply distributing an SOP is not enough. Provide training to ensure all employees understand how to use it and the importance of adherence. Emphasize that the "protocolo operacional padrão" is a living document, not a static rulebook.
- Monitor and Update: Regularly review and update SOPs to reflect changes in processes, technology, regulations, or best practices. Set a review schedule (e.g., annually or biennially). This ensures the SOP remains relevant and effective.
Platforms like Miro, as mentioned in the "Data Kalimat," offer templates that can simplify the creation process: "Na miro, compreendemos a importância da consistência e eficiência nas operações diárias, É por isso que criamos o modelo de pop (procedimento operacional padrão), Desenvolvido com cuidado e adaptado às necessidades do seu negócio, este modelo permite que sua equipe otimize processos e garanta que todos estejam na mesma página." Utilizing such tools can streamline the documentation and collaboration involved in SOP development.
Benefits Beyond Standardization: The Ripple Effect of SOPs
While the primary aim of a "protocolo operacional padrão" is standardization, its impact reverberates far beyond mere uniformity. The strategic implementation of SOPs triggers a cascade of benefits that profoundly influence an organization's operational health, financial stability, and long-term sustainability. These advantages extend into areas that might not be immediately obvious but are critical for holistic business success.
Streamlining Training and Onboarding
One of the most immediate and tangible benefits of robust SOPs is their role in transforming the training and onboarding process. Instead of relying on ad-hoc, verbal instructions that can vary wildly from one trainer to another, a "protocolo operacional padrão" provides a consistent, comprehensive, and readily available training manual. New hires can quickly grasp their responsibilities and the correct way to perform tasks, reducing the learning curve and accelerating their integration into the team. This not only saves valuable time for experienced employees who would otherwise be dedicated to repetitive training but also ensures that every new team member starts with the same foundational knowledge and adheres to the company's established best practices from day one. This systematic approach to training builds a more competent and confident workforce, reducing early-stage errors and improving overall team performance.
Beyond training, SOPs significantly enhance accountability and performance management. When every task has a clearly defined "protocolo operacional padrão," employees know exactly what is expected of them. This clarity minimizes misunderstandings and provides a clear benchmark against which performance can be measured. Managers can use SOPs to identify performance gaps, provide targeted feedback, and implement corrective actions. This objective framework fosters a culture of accountability, where employees are empowered to meet expectations and contribute effectively to organizational goals. Furthermore, in the event of an error or deviation, the SOP provides a documented baseline for investigation, helping to identify root causes rather than simply assigning blame.
Moreover, SOPs are instrumental in reducing operational risks and improving safety. Especially in industries where operations involve potential hazards, a detailed "protocolo operacional padrão" for every critical task is a lifeline. These documents outline safety precautions, proper equipment usage, emergency procedures, and handling of hazardous materials, significantly minimizing the likelihood of accidents, injuries, or costly operational failures. By embedding safety protocols directly into the workflow, SOPs create a safer working environment, protect employees, and reduce the financial and reputational costs associated with incidents. This proactive approach to risk management is invaluable for maintaining business continuity and ensuring employee well-being.
Finally, SOPs empower scalability and facilitate growth. As a business expands, the ability to replicate successful processes consistently across new locations, teams, or product lines becomes paramount. A well-documented "protocolo operacional padrão" provides the blueprint for this replication, ensuring that growth does not compromise quality or efficiency. It allows businesses to onboard new teams rapidly, maintain consistent service delivery across multiple branches, and integrate new acquisitions smoothly. This foundational structure is essential for sustainable growth, enabling organizations to scale operations without losing control or diluting their core values and standards. In essence, SOPs transform individual expertise into organizational knowledge, making the business more resilient, adaptable, and primed for future success.
Embracing the Future with SOPs: Continuous Improvement
In an era defined by rapid technological advancements, evolving market demands, and heightened consumer expectations, the concept of a "protocolo operacional padrão" remains not just relevant, but increasingly vital. However, the future of SOPs isn't about static documents; it's about dynamic, living tools that drive continuous improvement and adaptability. The journey of implementing SOPs doesn't end with their creation; it evolves into an ongoing cycle of review, refinement, and innovation.
The commitment to continuous improvement is where the true power of a "protocolo operacional padrão" is unleashed. Organizations must foster a culture where employees are encouraged to provide feedback on existing procedures. Who better to identify inefficiencies or suggest improvements than the individuals who execute these tasks daily? By actively soliciting input, businesses can ensure that their SOPs are not only current but also optimized for maximum effectiveness. This iterative process of "plan-do-check-act" (PDCA) is fundamental: plan the procedure, do it, check its effectiveness, and act on the findings to improve it. This ensures that the "protocolo operacional padrão" remains a relevant and powerful tool for operational excellence.
Furthermore, the future of SOPs will increasingly leverage technology. Digital platforms, interactive guides, and even AI-powered tools can make SOPs more accessible, engaging, and easier to update. Imagine an SOP that includes embedded videos, interactive checklists, or direct links to relevant software interfaces. Such innovations enhance usability, reduce training time, and ensure higher adherence rates. The ability to track usage, identify bottlenecks, and analyze performance data related to SOP execution will provide invaluable insights for further optimization.
Ultimately, a "protocolo operacional padrão" is more than just a set of instructions; it is a testament to an organization's commitment to quality, efficiency, and safety. It's about building a resilient, adaptable, and high-performing enterprise that can navigate challenges and seize opportunities. By embracing the principles of SOPs and committing to their continuous evolution, businesses can unlock their full potential, ensuring consistency and excellence in every operation, every single day.
As you embark on or continue your journey towards operational excellence, remember that the "protocolo operacional padrão" is your trusted ally. It's the blueprint for consistency, the foundation for quality, and the catalyst for continuous growth. Have you experienced the transformative power of well-implemented SOPs in your organization? Share your insights and challenges in the comments below, or explore our other articles on quality management and business process optimization to deepen your understanding.
- Colombia Primera A Standings
- Alamo Drafthouse Brooklyn
- Reign Judge
- Catalina Express
- Danny Rose Murillo

Procedimento Operacional Padrão
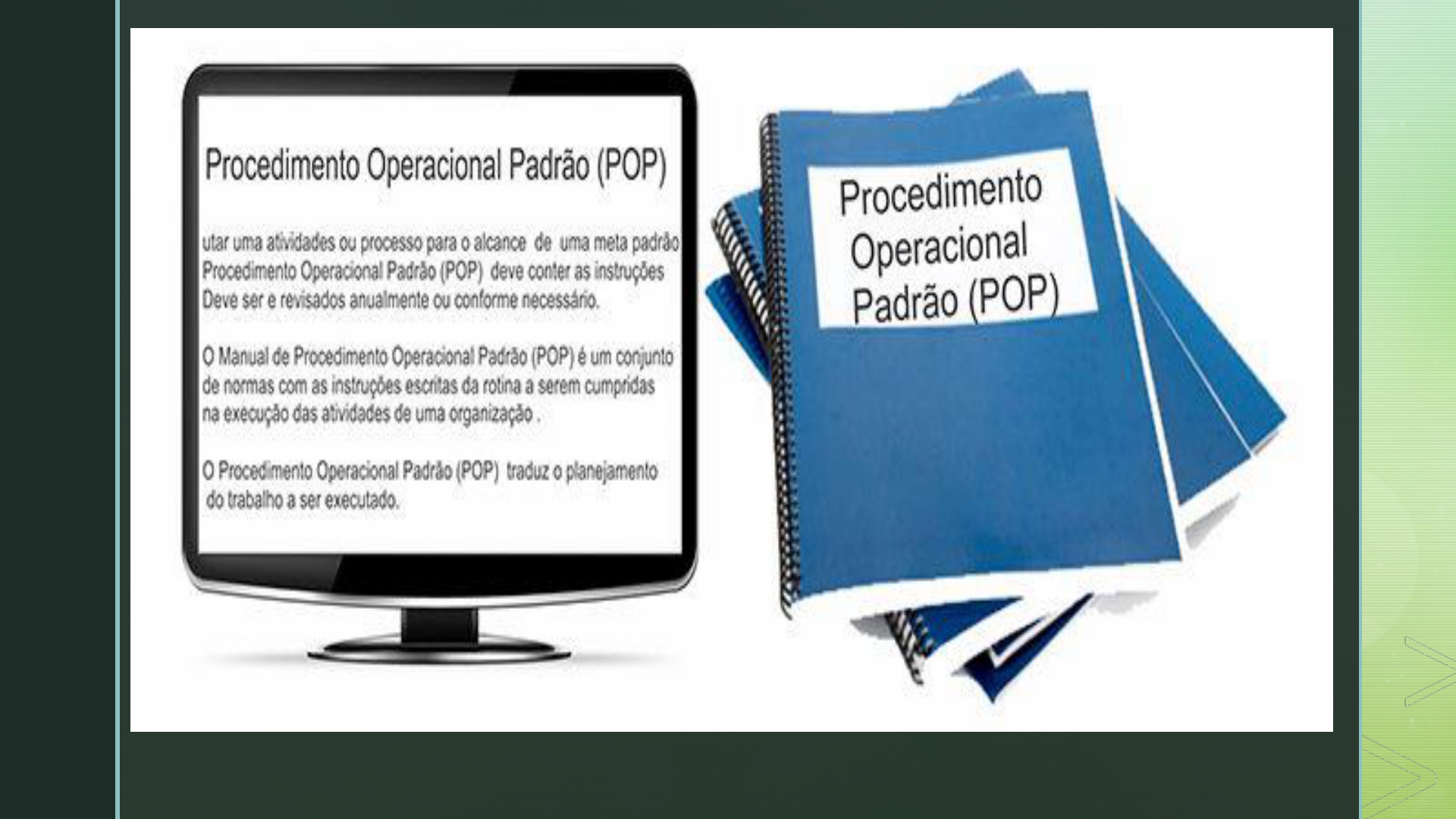
PROCEDIMENTO OPERACIONAL PADRÃO - Biossegurança
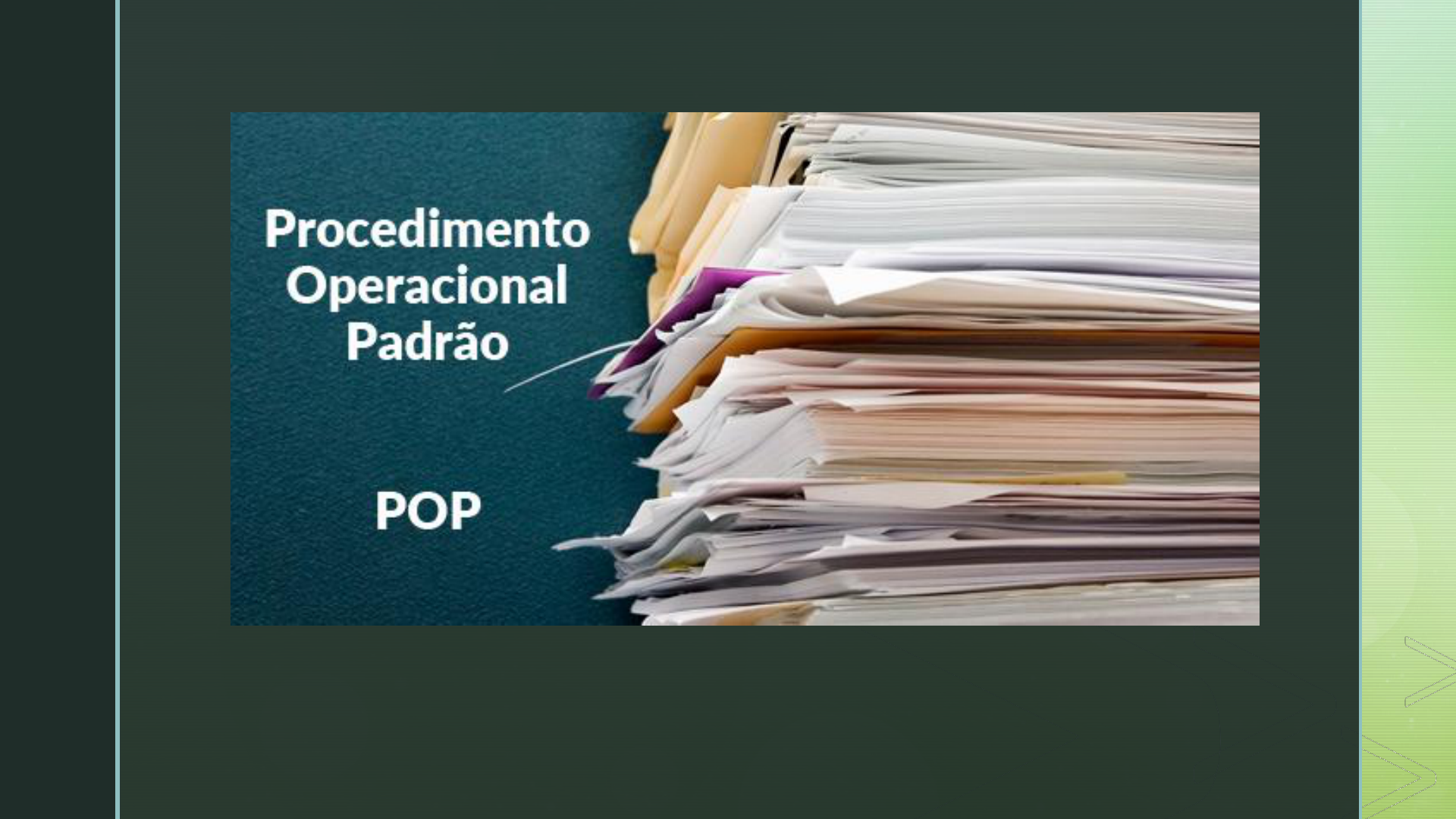
PROCEDIMENTO OPERACIONAL PADRÃO - Biossegurança